How wearables will power the next phase of workplace productivity
Wearables in the workplace
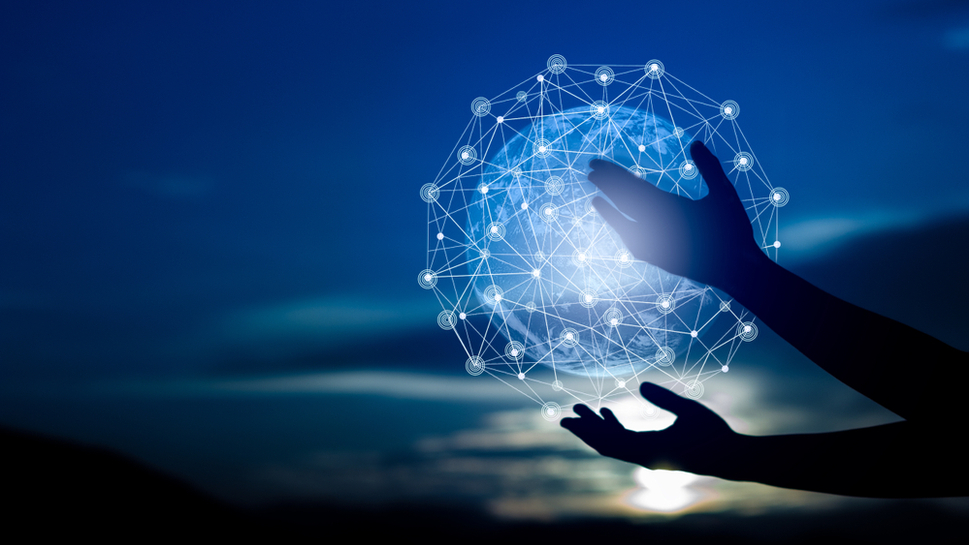
Last year, productivity in the UK fell at its fastest annual pace in five years. In fact, global workplace productivity has also weakened, with the annual growth in output per worker falling from 2.9 per cent to 2 per cent in the past decade. Not only has this caused a decline in employee engagement, but also a decline in economic growth.
Businesses need to reflect on their current operations and be open to changing the way they work. It’s equally critical for businesses to be attuned to their employees. Highly engaged teams are said to be 21 per cent more productive than their less engaged counterparts. As the world becomes increasingly digital, a vital factor for employee engagement, productivity and even talent acquisition and retention is technology.
Nick Offin is the Head of Sales, Marketing & Operations at Dynabook.
According to Microsoft, an overwhelming majority (93 per cent) of millennials state that a company possessing cutting-edge technology, services and solutions is an important consideration in accepting a job. Advances in enterprise technology therefore offer a win-win for companies, boosting the efficiency of business operations with the added benefits that employees feel more engaged, have more flexibility and ultimately work more productively.
One example that is seeing a growth in adoption is wearable technology, an industry expected to hit $54 billion in value by the year 2023. When we think of wearable technology today, we no longer just associate it with the consumer space such as smartwatches. There is also a significant opportunity for enterprises to gain from this growing trend.
Although yet to see mainstream adoption, wearable technologies such as assisted reality smart glasses promise to have a valuable impact on industries with a heavy reliance on frontline and field-based workers, such as in enterprise resource planning for warehousing, manufacturing, healthcare, aerospace and automotive. So, what is assisted reality? And how will it power the next phase of workplace productivity?
Assisted reality
AR refers to projecting additional information into a user’s field of vision, importantly hands-free. It differs from its perhaps better-known cousin, augmented reality, in that it does not change what the user is seeing, only adds an extra layer of information into their peripheral vision through diagrams, texts or videos. Industries reliant on frontline and field workers are increasingly adopting assisted reality smart glasses to empower workers and streamline workflows.
For example, in manufacturing it is not uncommon for product lines to change several times, multiple variants of a product to be in the same production, or even for different products to be on the same line. It’s therefore critical for warehouse employees to know which product they are processing, and which are the relevant instructions for assembly. Matching the two can be time intensive and can involve human error which ultimately slows the employee down if the wrong manual is selected.
Are you a pro? Subscribe to our newsletter
Sign up to the TechRadar Pro newsletter to get all the top news, opinion, features and guidance your business needs to succeed!
Assisted reality smart glasses, however, offer a faster, hands-free solution which ensures employees use the correct information for the given job order. Staff working in the warehouse can use the built-in camera or a hand-scanner to quickly identify the relevant instructions to a bar code and product. Not only this but they can receive updates to the manufacturing process and even call a supervisor so they can see any production issues in real time.
Production lines
Another example of how assisted reality can speed up production lines, improve workflows and benefit employees is through on-the-job training. Research shows after one-off training sessions, employee productivity spikes but returns to its previous level after 90 days. By using wearable technology, employees can receive ongoing, on-the-job training where technicians can be mentored live, in a real-world environment, via direct video support and instructions.
Using a Digital Workflows solution, technicians can refer to checklists, other text or diagrams through their head-mounted viewer, keeping their hands on tools at all times. Coupled with the Remote Expert solution, more senior technicians – whether on-site or not - can be on hand to offer training and advice on how to complete a task. The Manufacturing the Future Workforce report has shown how ongoing and flexible training courses – which can be used to upskill and reskill an existing workforce – deliver a steadier and more sustainable growth in workforce confidence and productivity.
In the world of manufacturing time is money, and so too is quality. Getting the right training and support quickly increases the efficiency of a workforce, not only on the front line but also of remote workers who would otherwise need to be present at a job. These are only a couple of examples that demonstrate how wearables are set to power the next phase of workplace productivity.
The impact of this technology is specific to the sector, organisation and role, but it’s easy to see the workplace appeal. While employees will enjoy using cutting-edge devices and the mobility that comes with it, enterprises will profit from streamlined processes, overall business growth and wearable technologies’ ability to empower the workforce of the future.
- We've featured the best identity management software for business.
Nick Offin is Head of Sales, Marketing and Operations at dynabook Northern Europe. He has the responsibility for sales teams covering end user segments including Public Sector, Corporate, Mid-market and Education sectors and Managed Partners across UK&I and the Nordics.